1. General Situation
Wire rod is one of the five major steel products, with an annual output of about 1 tons, accounting for 19% of the steel production in China. There are nearly 500 production lines domestically, of which more than 90% are at the third and fifth generation level of Morgan. Only a few enterprises, such as Baosteel, could keep abreast of contemporary level. Therefore, the upgrading of these third and fifth generation of high speed wire production lines is the main challenge facing China's wire rod industry。
The solution to this problem abroad is to adopt the technology of reducing sizing machines, which was developed by the Morgan Construction Company in 1995 and referred to as RSM for short. At present, more than 50 sets of RSM have been applied worldwide, while China's Baosteel reduced sizing unit is the first introduction of it in China。
However, applying RSM to most of the high speed wire mills in China is not feasible for the following reasons.
1)High construction costs and long-term supply monopoly of spare parts. Besides the service is not timely;
2) Complex equipment and technology overload is not suitable for China's many high-speed wire production line;
Therefore, it is necessary to develop advanced and practical technology in order to accommodate the actual situation of most wire mills in China. The double rack sizing machine, or MFM emerged at the right moment. With the complete technology of MFM, the question is who dares to be the first one to use? which is key to the popularization and application of this technology。
Jiangsu Yonggang group bravely takes the lead. through two years of relentless efforts and cooperation of the departments concerned , and finally in December 8, 2015, the first domestic double rack reducing sizing mill (MFM) was put into operation successfully, on 8, December,2015, delivering a significant result:
1)The rolling speed exceeded the 100m/s mark;
2)The dimensional accuracy and performance have reached international advanced level;
3)In the year of 2016 alone, the revenue grew by 28,880 million yuan, exports earning reached 130 million yuan;
Practice shows that the performance of MFM is no worse than that of RSM by Morgan , and even more convenient, suitable for a large number of Chinese high speed wire plants, with only 1/3 ~ 1/5 of previous cost.
The research and development of this project meets the upgrading requirement of many high-speed wire factories, and solves the difficult problems faced by the wire rod industry。
2.Process layout and parameter
Jiangsu Yonggang group applied double rack reducing sizing mill and completed commissioning in December 8, 2015 which is mainly used for φ 5.5, φ 6.5, φ 7, φ 8 specifications of wire rod production。
2.1,Process layout
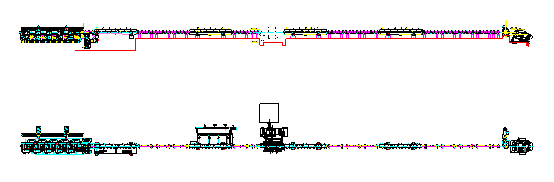
Fig. 1 layout of MFM
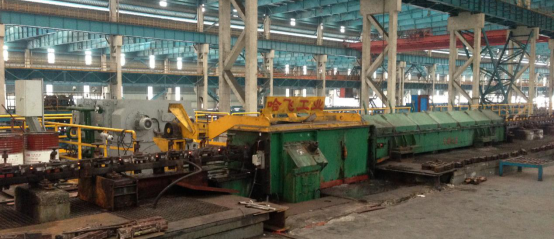
Fig 2 production site
2.2 Old line: double rack reducing sizing mill is placed in the middle of water cooling equipment, delivering the following benefits.
Ensuring the rolling speed: 105m/s;
Improving the production output by more than 15%;
The deformation induced ferrite transformation can be realized by rolling at 800℃, and ultra-fine grained steel can be obtained to reduce energy consumption and reduce rolling costs,ensuring low investment, high rate of return, short investment recovery time.
1.2 New line: 8 finishing mills (All 8 "rollers) and 2 MFMs (new 8”rollers)
The rolling torque increases, reduce the number of roller box and backup machine;
Ensuring the rolling speed: 105m/s;
It can reduce the rolling temperature by above 100 degrees, obtain ultra-fine grained steel, reduce energy consumption and reduce rolling costs.
3, the Implementation and Effect
When MFM applied , not only the rolling speed has been significantly improved, rod organization, iron oxide, surface red rust problem has obviously addressed.
1 Rolling Speed
After applying MFM, the rolling speed of the small size products has been improved obviously, as shown in table 1.
Table 1, rolling speed comparison
Production speed m/s | Ø5.5 | Ø6.5 | Ø7 | Ø8 |
Before Applying MFM | 85 | 85 | 85 | 64 |
After Applying MFM | 102 | 102 | 100 | 80 |
2. Production Output
2.1Increased production of round steel with φ5.5 and φ6.5 specifications and reduced costs
Table 2, hourly output comparison
Specifications(mm) | φ5.5 | φ6.5 |
Hourly Output before Applying MFM | 56 | 75 |
Hourly Output after Applying MFM | 60 | 83 |
Output Increase Percentage(%)) | 7.1 | 10.7 |
Cost Decrease per ton(yuan/t) | 2.5 | 11.3 |
As we can see from table 1, the hourly output of ф5.5mm and ф6.5mm steel increases by 7.1% and 10.7% respectively,. Although MFM may induce power consumption increase, other costs (such as labor, water consumption, gas consumption and so on.) do not rise, combined with the increase in production, the total cost per ton is declined. The cost of φ 5.5mm, φ 6.5mm per ton is reduced to 2.5 yuan / ton and 11.3 yuan / ton respectively.
2.2 Output Increase and Cost Decrease of Rebar φ8 HRB400
(Shown in Table 3)
Accounting item | Daily Capacity(T) | Estimated annual capacity (ton) | Rolling cost (yuan / ton) | Alloy cost (yuan / ton) |
Finished rolling speed 65m/s | 1650 | 594000 | 120.0 | 126.0 |
Finished rolling speed 80m/s | 2100 | 756000 | 112.5 | 123.0 |
Difference | +450 | +162000 | -7.5 | -3.0 |
Rebar φ8HRB400 finished rolling speed reaches 80m/s and daily output 2100ton. Annual capacity increased by about 162 thousand tons. Steel rolling cost per ton can be reduced by 7.5 yuan / ton, the cost of alloys can be reduced by 3 yuan / ton, the total cost per ton add up to 10.5 yuan / ton.
In the production increase at the same time, product quality has also improved. Thread steel φ 8 HRB400, from the trial production process of the test results, the grain size from the original 7-8 to 9, and more refined grain makes the steel structure more uniform, mechanical performance more stable.
3. Quality Improvement
3.1 products 3.1 SWRCH22A cold heading steel Widmanstaten problems improved
The problem of Widmanstatten structure of cold rolled steel SWRCH22A has been significantly improved. The mechanical properties of the Widmanstatten structure and the wire rod structure are quite different, resulting in uneven deformation and even fracture of the wire rod during the drawing process. The problem of Widmanstatten structure of cold rolled steel SWRCH22A has been significantly improved after applying MFM. Previously, the frequent occurrence of large-scale Widmanstatten structure causes fractures during the drawing process. On the condition of MFM applied, the similar quality problems haven't been heard so far.
The 120 samples of the finished product of φ5.5 and φ6.5 specifications SWRCH22A before and after applying MFM are taken to observe the microstructure of these samples by optical microscopy, and the Widmanstatten structure is evaluated. The results are shown in Table 4 and Figure 3.
Table 4 shows SWRCH22A Widmanstaten ratio before and after the use of MFM
The level of Widmanstaten structure | No | Level 1 | Level 2 | Level 3 | Level 4 |
The proportion before applying MFM | 70 | 15 | 5.8 | 5.0 | 4.2 |
The proportion after applying MFM | 72 | 18.7 | 7.0 | 1.5 | 0.8 |
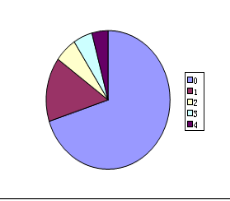
before the use of MFM
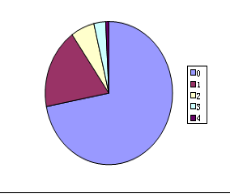
after the use of MFM
From table 4 and figure 3 we can clearly see after the use of MFM, the proportion of level 3 and level 4 Widmanstaten structure is significantly reduced.
The superheated medium carbon steel and low carbon steel austenite have a large grain size, and the widmannsttten structure is easily generated at a relatively fast cooling rate. The mechanical properties of the widmannsttten structure are quite different from those of the steel matrix, leading to deformation in the subsequent processing. After applying the MFM, the parts can be cold-rolled into the MFM mill for final rolling. The low-temperature rolling can make the austenite grains finer and can effectively inhibit the widmannsttten structure.
The reason of the widmannsttten structure formation is that the austenite grains are coarse at high temperature, and fast cooling rate. The iron and carbon atoms do not reach enough diffusion during the cooling process, forcing the crystalized ferrite generated along the austenite grains. When there is no MFM mill, the final rolling temperature of the wire rod is up to about 1050 °C and needs to be strongly cooled to 900 °C after rolling. In this process, the QTB demand is large, the cooling is quite uneven. In the place of the steel bend (hole width), the cooling rate is too fast, so the widmannsttten structure is formed on both sides of the base circle of the wire rod. After applying MFM mill, the rolling stock can be used to reduce the sizing unit at a low temperature. The final rolling temperature can be as low as 930 °C. After rolling, only a small part needed QTB process in order to reach the temperature of 900 °C. The temperature difference before and after QTB process is small, and the cooling rate is low, ensuring cooling process to be more evenly, so the problem of widmannsttten structure is greatly improved.
3.2 scale structure
Previously, customers have always reflected that the wire rod oxide scale is not good, showing the characteristics of thin, brittle, sticky, and difficult to remove. It is not easy to remove after pickling and mechanical peeling. The scale is easy to cut and cause fracture during the drawing process. Besides,the mold loss is large.
The final rolling temperature, spinning temperature, air-cooling process, etc. are the main factors affecting the thickness of the wire rod scale. After the MFM rolling mill is put on the line, the rolling temperature of the rolled steel and cold-rolled steel into the MFM rolling mill can be controlled to 860~ 900 ° C, spinning temperature 910 ± 15 ° C, can well control the amount of cooling after rolling, thus the cooling process can be more even, the scale structure is more compact and complete.
The dense and complete oxide scale is more conducive to mechanical peeling, and the surface of the wire rod does not leave iron oxide skin after peeling. Since the MFM mill is put into operation, there has been no such feedback that the scale is difficult to remove.
Figures 4 and 5 are comparison of oxide scale before and after applying MFM mill.

Cold heading steel oxide structure
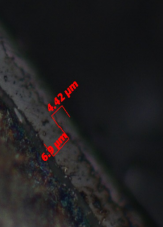
Medium and high carbon steel oxide scale structure
3.3 The problem of red rust on the surface of the wire rod is improved very well.
In the past, when the temperature of the production of cold heading steel and medium and high carbon steel was about 900 °C, the red rust on the surface of the wire rod was serious, which affected the appearance quality of the wire rod. Since the floating rust is loose, the surface of the wire rod is corroded from the floating rust to the base after the steel bar is placed in the stock for a period of time. Such a wire rod is subjected to peeling and pickling, and the surface quality is poor, which affects drawing.The main reason for the red rust on the surface of the wire rod is that the flow rate of water required after rolling is large, and the temperature difference between water cooling is large. The impurities in the cooling water are attached to the surface of the steel bar,affecting the cooling of the steel bar, and the surface of the steel bar is abnormally oxidized, forming a red loose Fe2O3 On the surface.After applying the MFM mill, the rolled parts can be cold-rolled into the MFM mill for final rolling. After rolling, the wire temperature can be met as long as the water is slightly worn. There is less floating rust formed on the surface of the steel with a small amount of water, thus the surface quality of the wire rod is improved.
3.4 The hardness of cold heading steel drops significantly
After the MFM mill is used, it can realize low temperature final rolling and low temperature spinning. The slow cooling after rolling can reduce the hardness of cold heading steel. The hardness of the 10B21 finished product before and after the MFM mill applied as well as products produced by five imported Morgan were taken into test, and found that the hardness was found to be significantly lower than before.
Table 10 shows hardness comparison
| Line four before the use of MFM | Line four after the use of MFM | Line five sixth generation of reducing sizing mill by Morgan |
Hardness average | 78.6 | 75.0 | 73.3 |
Fluctuation range | 73.1-84.4 | 72.3-79.7 | 68.3-77.1 |
unit: HRB
3.5 Fine-grained reinforced HRB400 steel wire rods by controlled rolling and controlled cooling
After the MFM rolling mill was put on the line, some of the screw 8HRB400 was test rolled. it is shown that the 400MPa grade steel bar strengthened by fine grain strengthening through low temperature controlled rolling and air cooling after rolling. Not only the mechanical properties of the finished product are stable, but also the rolling speed is greatly improved.
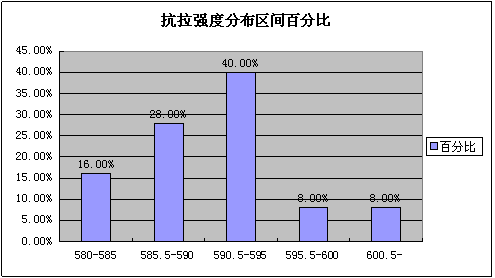
Figure 6 screw 8HRB400 tensile strength histogram
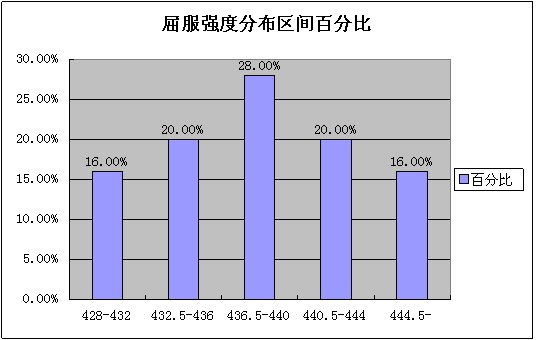
Fig. 7 yield strength histogram
It can be clearly seen from Fig. 6 and Fig. 7 that the mechanical properties of the screw 8HRB400 when the MFM mill applied are quite stable, which is not lower than the national standard, and the yield strength is mostly stable between 430 and 445 MPa, and the tensile strength is mostly stable between 585-595MPa.
4、Economic performance
Economic benefits: 10000 yuan (RMB) |
Total project investment: | 1000 | Payback period (month) | 3 |
column Particular year | New output value | New profits and taxes | Income foreign exchange | Income (total cost) |
2016 | 18730.076 | 3800.542 | 13111.05 | 2885.58 |
2015 | 0 | 0 | 0 | 0 |
2014 | 0 | 0 | 0 | 0 |
Cumulative | 0 | 0 | 0 | 0 |
Calculation basis of each column |
1.The basis for the calculation of direct economic benefits: The specifications of Φ5.5 and Φ6.5 are calculated according to the original annual output of 180,000 tons. The annual cost reduction is shown in Table 6. This cost includes water and electricity consumption as well as labor costs.Table 6 is accounted for according to the benefits of the cost reduction after using the MFM mill. Specifications(mm) | Φ5.5 | Φ6.5 | the original annual output (10,000 tons) | 18 | 18 | Reduced cost per ton (yuan / ton) | 4.0 | 4.9 | Annual profit (10000 yuan) | 18*4.0=72 | 18*4.9=88.2 | Total (10000 yuan) | 72+88.2=160.2 |
2, specificationΦ5.5, Φ6.5 round steel production yields considerable benefits, according to the average price of ordinary industrial materials 3468 yuan / ton, the average ton steel profit 100 yuan / ton, See Table 7. Table 7 shows Benefits of increasing production of specification 5.5 and 6.5 with the use of the MFM mill Specifications(mm) | Φ5.5 | Φ6.5 | Total | original annual output (10000 tons) | 18 | 18 | 36 | output increase% | 11.1 | 15.3 | / | Annual profit (million) < /p> | 18*11.1%=1.998 | 18*15.3%=2.754 | 4.752 | Annual profit (million) | 1.998*3468=6929.064 | 2.754*3468=9550.872 | 16479.936 | Annual profit (million) | 1.998*100=199.8 | 2.7544*100=275.44 | 475.24 |
3. The production of some high value-added products will bring more profits. The profit of this part of the products will reach an average of 300 yuan/ton, and other low-end products will be replaced, resulting in a profit difference of about 200 yuan/ton. The new output value of this part is the profit margin, as shown in Table 8. Table 8 shows output value and profits of high value-added Products in 2016
| Production (million tons) | The new value (wanyuan) | φ5.5mm SWRCH22A/B/Ti | 0.5953 | 119.06 | φ6.5mm SWRCH22A/B/Ti | 5.9737 | 1194.74 | φ5.5mm SWRH72A/B-82A/B | 4.1591 | 831.82 | φ6.5mm SWRH72A/B-82A/B | 0.5226 | 104.52 | Total | 11.2507 | 2250.14 |
In summary, the annual newly added output = the output value of the increased production part 164,799,600 yuan + the profit difference generated by the high value-added products 2,251,100 yuan = 187,770,600 yuan. Newly added profit = profit generated by increased part 4,752,400 yuan + profit difference of high value-added products 2,502,140 yuan = 2,725,380 yuan. The value-added tax is calculated at 17%, the income tax is calculated at 25%, and the other taxes are calculated at 1.7%. The newly added tax generated is calculated to be 1,075,162 yuan. Therefore, the newly added profits and taxes = 2,725,380 yuan + 10,715,162 yuan = 3,805,402 yuan。According to the export volume of 70% of the output by fourth branch of wire factory, the income generated by foreign exports = newly added output value of 18730.076*70%=13111.05 million. Total increased income = new profit of 27.2538 million yuan + cost reduction of 1.602 million yuan = 28,850,800 yuan |
5、Innovation point
1、Innovation in technology, line and process
The reducing sizing mill RPM by Morgan is driven by an AC variable frequency motor with a voltage of 3300V and a power of 4500 kW. The transmission passes through a complex gearbox with 9 gears and various shifting gears to meet various specifications. However, many wire rod factories in China do not such many specifications and do not demand so many shifts. Our double reducing sizing mill is a two-frame MFM with only two gears, which fully meets the shifting requirements of most wire rod factories in China. The main motor is only one 2500KW AC motor. With such a simple configuration, we can upgrade most of third and fifth-generation production lines to the contemporary (sith generations) level. Figures 8 and 9 are schematic diagrams showing the transmission structure of the Morgan RSM and of the MFM.
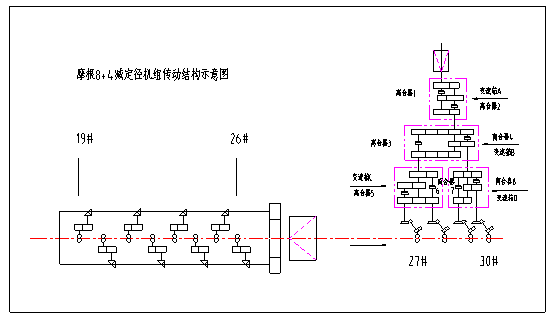
Schematic diagram of transmission structure of RSM
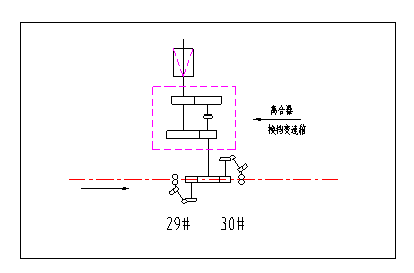
Schematic diagram of transmission structure of MFM
In short, RSM is complex in structure and technological overload, and also high price monopoly, while the technical methods adopted by this project are advanced, practical, based on national condition and easy to promote. Secondly, in terms of technology, the difficulty of this project exceeds that of others. It is difficult to arrange the reducing sizing mill within the limited distance between the existing finishing train and the laying machine to achieve controlled rolling, and to achieve high-speed continuous rolling with the finishing mill to maintain a reasonable pile-up relationship. It is very difficult to control.
2. Innovation of electronic control system
(1) Breaking through the routine. It is the first time in both home and abroad that the low-voltage frequency conversion system is applied on the reducingand sizing mill to replace the foreign monopoly medium-voltage frequency conversion system. With the AC690V low-voltage control scheme, the investment cost of electrical equipment is about 1/2 or less of the foreign medium-voltage scheme. However the performance is same, with China-made parts.
(2) Simple structure, easy maintenance and easy to master. Different from the AC3300V medium voltage control scheme abroad, this scheme adopts low-voltage AC690V inverter with high-performance multi-machine transmission and modular transmission. The medium voltage frequency conversion system is more complicated. Once a fault occurs, it is difficult for the technician to quickly diagnose the cause , and the problem solving time is long and the cost is high.
(3) The supply cycle is greatly shortened. The domestic supply cycle is about two to three months, while the imported equipment has an ordering period of more than half a year.
(4) The control software package developed by the company independently solves the coordination and matching of the rolling speed with the upstream finishing mill, and ensures the speed setting and control precision requirements of the automatic rolling process.
3、Innovation of mechanical equipment
(1)The structure adopts a single speed-up mechanism, which simplifies the transmission structure, improves reliability, simplifies operation and makes it easy to maintain and use. Morgan's reducing sizing machine consists of an AC motor that drives two 230mm reducers and two 150mm sizing machines through a single gearbox which contains nine clutches. Danieli's dual-module reducer has a total structure of four passes and two modules. Two motors drive two gearboxes respectively, and electrical interlocking is used to achieve speed matching. Morgan and Danieli's reduction and sizing machine transmission structure are relatively complicated, especially the utilization rate of the 9-speed clutch structure is quite low, while Danieli's dual motor input relies on electrical interlocking for speed matching mode, and the accuracy of automation control and of the hole type process plan is fairly high. The project adopts the transmission structure of which a motor is directly connected to the transmission through the gearbox. The gearbox only has one clutch device. The product specifications and rolling speed are divided into two levels, which can fully meet the rolling process requirements. The relative structure of the project is simple and practical, and the variety specifications and rolling speeds are reasonable and reliable.
(2) With regard to transmission, in order to improve the reliability, stability and carrying capacity, the innovative new gear system is employed in the high-speed transmission. Improving the stability of the drive is key to reducing noise and vibration, lengthening the life, and improving the performance. In order to meet the requirements of high-speed rolling, the transmission box of this project applys the compact design of the whole structure. The transmission structure adopts a pair of spiral bevel gear structures with a cone angle of 45°. In this item, Gleason is used for high-speed gears. The traditional design of the tooth system has made a breakthrough, adopting a new high-capacity tooth form, ensuring the load-carrying capacity, running stability and reliability of the whole machine equipment.
(3)(3) The high-speed roller shaft string assembly structure adopts a self-centering form, which addresses the problem of equipment unstability caused by unbalanced quality due to improper assembly and use. The roller box adopts the insert type structure, while the cantilever roller ring and the eccentric sleeve mechanism in the box body are used to adjust the roll gap. The eccentric sleeve is equiped with an oil film bearing and a roll shaft, and the roll ring is fixed by a taper sleeve at the end of the cantilever. When the rolling mill is running at 105m/s, the rolling shaft speed reaches 9000r/min. The dynamic balance accuracy of the high-speed shaft has a great influence on the running stability of the equipment. The G1 dynamic balancing technology is utilized here. The self-centering assembly supporting structure is applied on the shaft string assembly, which not only solves the problem of dynamic balance instability, but also simplifies the disassembly and assembly operation and improves the maintenance efficiency.
(4)Simplifying the rolling pass process, and directly using the finished hole type of the original finishing mill. In this project, the elliptical-round rolling pass system with traditional wire rod and large sharing capability is adopted in the hole design. Since the project adopts 230mm roller box, the maximum rolling force is 330kN, which has a large reduction ratio. The section can be flexibly adjusted to a large extent, which greatly simplifies the hole system of roughing rolling, medium rolling, pre-finishing and finishing rolling. At the same time, the unit can directly use the finished hole type of the finishing rolling mill, thus the little work of fine-tuning of the remaining fine-rolling hole types is only needed for production. The process is mature with simple introduction and fast production.
Figure 1-6 is the structural drawing of MFM equipment
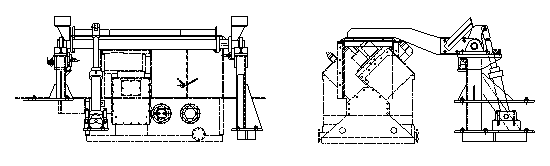
Figure 1MFM outline drawing of rolling mill
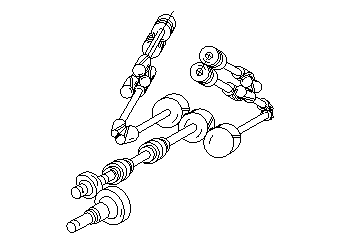
Figure 2 transmission structure drawing
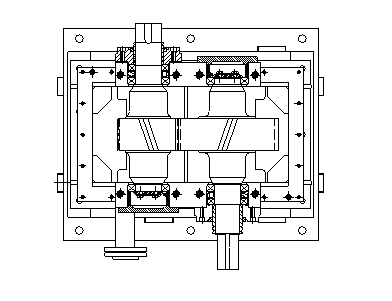
Figure 3 structure of speed increasing box
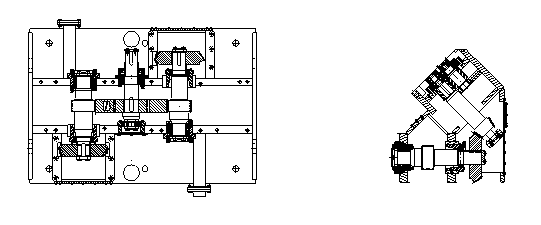
Figure 4 transmission box structure drawing
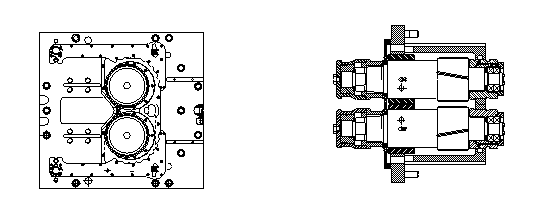
Figure 5 roll box structure drawing
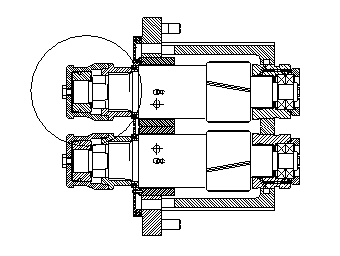
Figure 6 self centering structure of high speed axle string